Automotive Steel: Driving the Future
2023-05-22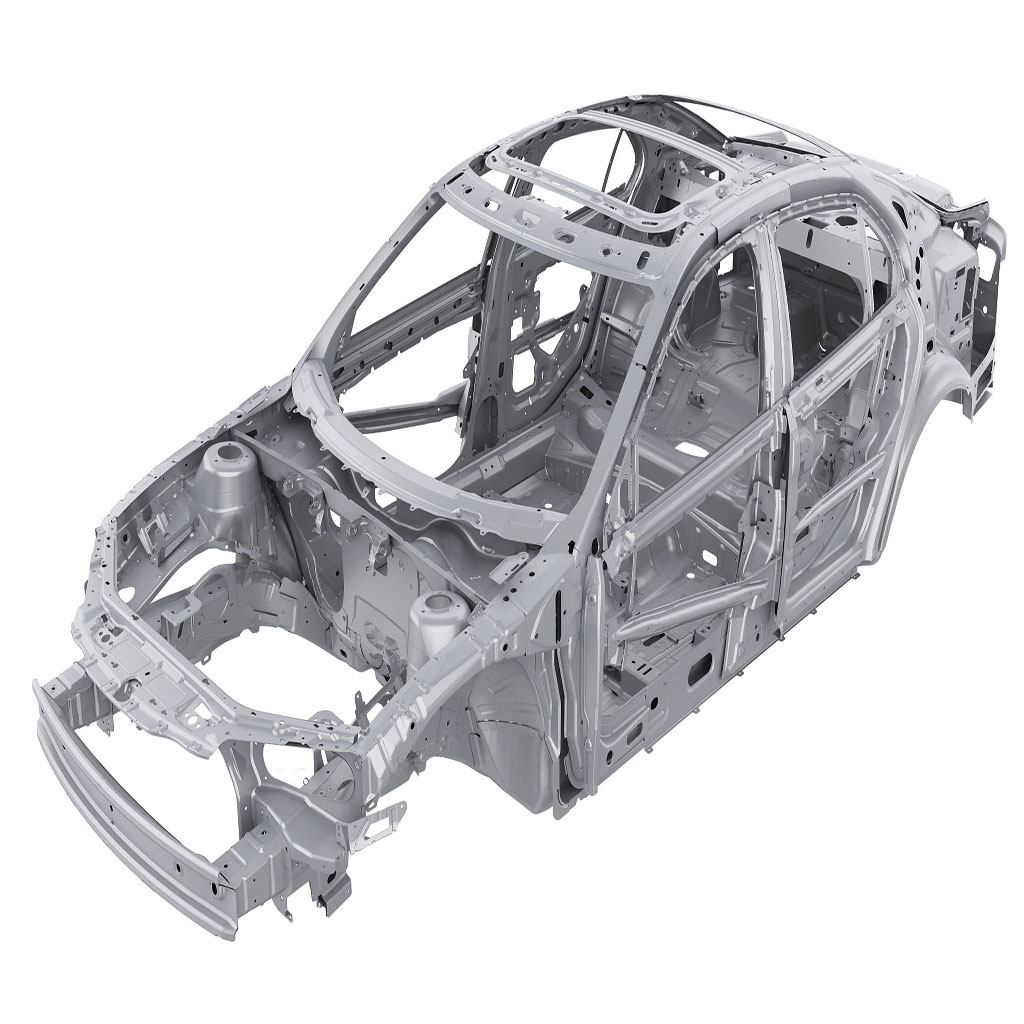
What is automotive steel and its importance to the automotive industry
Automotive steel refers to the various types of steel used in the manufacturing of automobiles. It plays a crucial role in the automotive industry due to its unique properties and importance in ensuring vehicle safety, performance, and cost-effectiveness. Here are some key aspects of automotive steel and its significance:
1. Strength and Safety: Steel is chosen for its high strength-to-weight ratio, making it an ideal material for constructing the structural components of vehicles. It provides the necessary rigidity and crashworthiness to ensure occupant safety during collisions. Advanced high-strength steels (AHSS) are specifically designed to offer exceptional strength and energy absorption, improving overall vehicle safety.
2. Lightweighting: The automotive industry is constantly striving to reduce vehicle weight in order to enhance fuel efficiency and reduce emissions. Lightweighting is achieved by using advanced steel grades that offer high strength while maintaining low weight. These steels allow car manufacturers to meet stringent fuel economy standards without compromising safety.
3. Cost-Effectiveness: Steel is a cost-effective material compared to alternatives like aluminum or carbon fiber composites. It has a relatively low raw material cost and is readily available in large quantities. Automotive steel’s affordability makes it an attractive choice for mass production, enabling automakers to offer vehicles at competitive prices.
4. Formability and Manufacturability: Steel’s formability and manufacturability are key advantages in the automotive industry. It can be easily shaped into complex geometries, allowing for the creation of intricate vehicle designs. Steel’s ability to be stamped, welded, and assembled with relative ease facilitates efficient mass production on assembly lines.
5. Corrosion Resistance: Automotive steel often undergoes various coatings and treatments, such as galvanization or painting, to enhance its corrosion resistance. This helps protect the vehicle’s body and structural components from rust and extends its lifespan, particularly in regions with harsh weather conditions.
6.Recyclability: Steel is highly recyclable, making it an environmentally friendly choice. At the end of a vehicle’s life cycle, steel components can be easily recovered and recycled, reducing waste and conserving resources.
Overall, automotive steel provides the necessary strength, safety, lightweighting, cost-effectiveness, and manufacturability required by the automotive industry. Its continuous development and incorporation of advanced steel grades contribute to the ongoing improvements in vehicle performance, efficiency, and sustainability.
Historical Development of Automotive Steel
The historical development of automotive steel can be traced back to the early days of the automotive industry. Here is a general overview of the key milestones in the evolution of automotive steel:
Early Years (Late 19th Century): The first automobiles were built using primarily wrought iron and steel. These early vehicles had relatively simple structures and used steel components for their chassis, axles, and wheels.
Introduction of Mass Production (Early 20th Century): With the advent of mass production techniques, such as the assembly line pioneered by Henry Ford, there was a growing demand for materials that could be efficiently manufactured and assembled. This led to advancements in steel production and processing techniques to meet the needs of the burgeoning automotive industry.
Introduction of Mild Steel (1920s-1930s): In the 1920s and 1930s, mild steel became the dominant material in automotive construction. Mild steel offered good strength and formability at an affordable price, making it suitable for mass production. It was widely used in car bodies and structural components.
Advancements in Steel Processing (1940s-1950s): During World War II, advancements in metallurgy and steel processing techniques were made to meet the demand for military vehicles. These advancements, such as the development of new alloying elements and heat treatment processes, laid the foundation for future improvements in automotive steel.
High-Strength Steels (1960s-1970s): In the 1960s and 1970s, there was a shift towards the use of high-strength steels in automotive applications. High-strength low-alloy (HSLA) steels, which offered improved strength and formability, started to be used in critical structural components, such as chassis and frames.
Introduction of Advanced High-Strength Steels (AHSS) (1980s-1990s): The 1980s and 1990s saw significant advancements in steel technology, leading to the development of advanced high-strength steels (AHSS). AHSS, including dual-phase (DP) steel, transformation-induced plasticity (TRIP) steel, and others, offered even higher strength and improved crash performance while maintaining good formability. AHSS started to be used in safety-critical components, such as pillars and door reinforcements.
Lightweighting Initiatives (2000s-Present): In recent decades, automotive manufacturers have been focused on lightweighting to improve fuel efficiency and reduce emissions. This has led to the development of ultra-high-strength steels (UHSS) with exceptional strength and lightweight properties. UHSS, including press-hardened steel and other advanced alloys, are used in critical areas of the vehicle structure, providing a balance between strength and weight reduction.
Future Trends: The automotive industry continues to explore new materials and technologies to further enhance vehicle performance, safety, and sustainability. This includes the adoption of alternative materials like aluminum, carbon fiber composites, and advanced engineering plastics in combination with steel to achieve optimal results.
The historical development of automotive steel reflects the ongoing efforts to meet the evolving demands of the automotive industry, such as safety, cost-effectiveness, manufacturability, and lightweighting. Advancements in steel production, processing techniques, and alloy development have contributed to the continuous improvement of automotive steel grades and their applications.
What types of steel are used in cars?
Several types of steel are used in the construction of cars due to their desirable properties such as strength, durability, and cost-effectiveness. Here are some common types of steel used in automotive applications:
1. Mild Steel: Also known as low-carbon steel, mild steel is used extensively in car bodies and structural components. It offers good strength and formability while being relatively affordable.
2. High-Strength Low-Alloy (HSLA) Steel: HSLA steel contains small amounts of alloying elements such as vanadium or niobium, which enhance its strength without sacrificing formability. It is used in various structural parts, including chassis components.
3. Advanced High-Strength Steel (AHSS): AHSS refers to a group of steels that exhibit exceptional strength and formability. These steels are often used in critical safety components like pillars, door reinforcements, and crash structures. Examples include dual-phase (DP) steel, transformation-induced plasticity (TRIP) steel, and martensitic steel.
4. Ultra-High-Strength Steel: This category includes steels with extremely high strength, typically achieved through advanced metallurgical processes. Ultra-high-strength steels are used in areas where maximum strength is required, such as safety-critical parts. Examples include boron steel and press-hardened steel.
5. Stainless Steel: Stainless steel, known for its corrosion resistance, is used in various automotive applications, particularly for exhaust systems, decorative trims, and components exposed to harsh environments.
6. Galvanized Steel: Galvanized steel is coated with a layer of zinc to provide corrosion resistance. It is commonly used in areas prone to rusting, such as undercarriage components and body panels.
7. Dual-Phase Steel: Dual-phase steel combines the strength of martensitic steel with the formability of ferritic steel. It is used in structural parts that require high strength and crash resistance.
8. Electrical Steel: Electrical steel, also called silicon steel, is used in the production of electrical components like motors and generators.
It’s important to note that the specific steel types used in cars can vary depending on the manufacturer, model, and intended application of the vehicle. Different combinations of steel grades are employed to optimize the balance between strength, weight reduction, safety, and cost-effectiveness.
The company’s main business is general GMW standard, Fiat EFE standard, Volvo VDA standard, Nissan NEN standard, Volkswagen VW50065, Ford WSS-M and other standard series of automotive steel.
Looking forward to your inquiry!